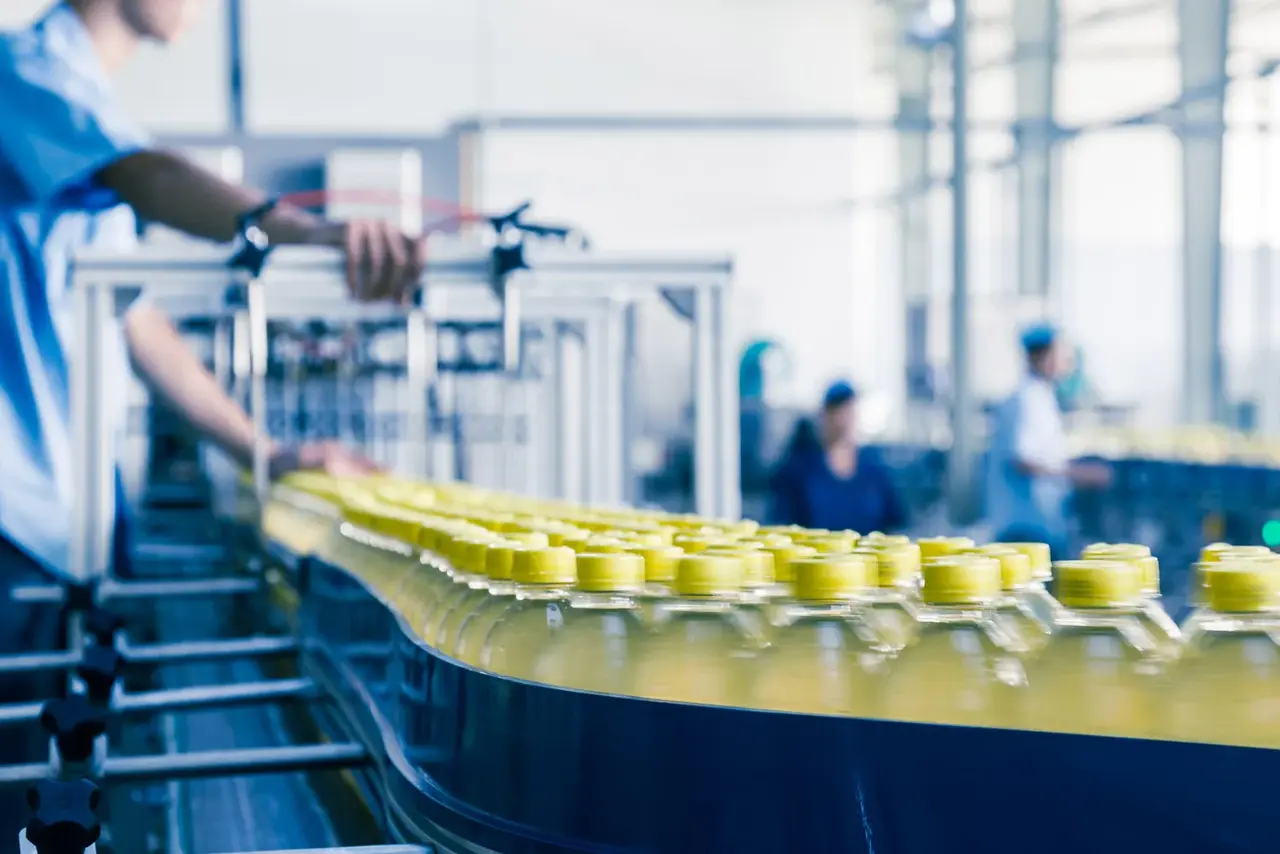
Quality Management in the Consumer Goods Industry / Packaging Industry
References from the Consumer Goods Industry
QM Solutions for the Consumer Goods Industry
Checklists
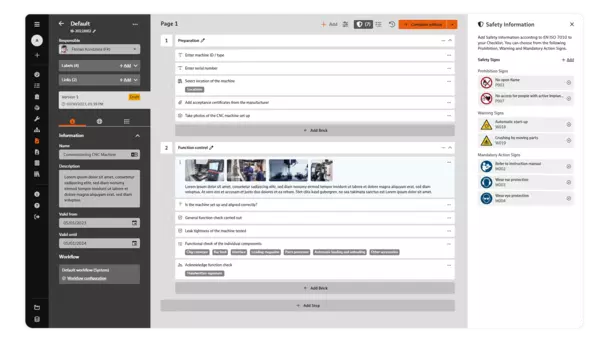
Creating checklists in BabtecQ Go is child's play thanks to the no-code modular system.
Commissioning, process sequences, assembly instructions, acceptance inspections: There are certainly many use cases in your company where checklists can provide effective support.
In the browser-based BabtecQ Go, you can easily digitize, share and use all your checklists. Standardize processes and create transparency for your employees. All the knowledge gained from your records is reliably incorporated into your continuous improvement process (CIP).
Incoming Goods Inspection / Outgoing Goods Inspection
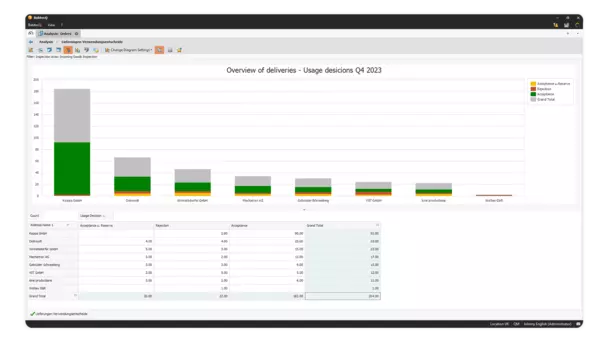
With BabtecQ, you can create clearly structured, efficient test sequences and support the correct execution of the test with visual assistance.
Companies in the consumer goods industry work with a large number of suppliers. Incoming goods inspections enable them to ensure that the materials supplied by the suppliers meet the required quality standards. Outgoing goods inspections, on the other hand, ensure that the finished products fulfil the defined specifications before they are delivered to the customer.
As a rule, these inspections involve a great deal of effort. BabtecQ supports you with your incoming goods inspection / outgoing goods inspection and enables you to carry out the inspections efficiently and in a time-saving manner.
Complaints Management
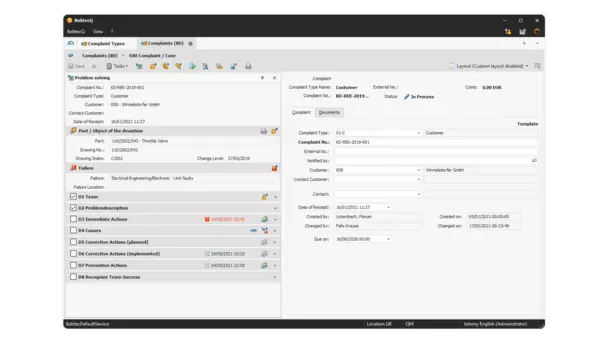
Complaints management in BabtecQ makes it easier for you to consistently analyze complaints.
In the consumer goods industry, the traceability of products and batches is of great importance. If a product needs to be recalled due to quality issues, a well-established complaints management enables the quick identification of affected batches and the coordination of the recall to minimize the impact on consumers and the company's image.
Complaints management in BabtecQ supports you in establishing a sophisticated complaints management.
Task Management / Action Management
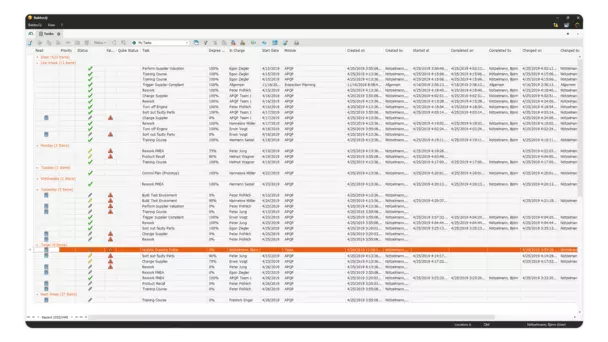
Whether immediate actions implemented, corrective actions introduced or preventive actions: In the dialogue for processing an action, you document relevant information in a central location.
Companies in the consumer goods industry are constantly receiving feedback from customers, be it through complaints, product reviews or social media. Efficient action management makes it possible to collect and analyze this feedback and take appropriate actions to improve quality.
Use the task and action management of the BabtecQ QM software to centrally manage and track your tasks and actions.
Audit Management
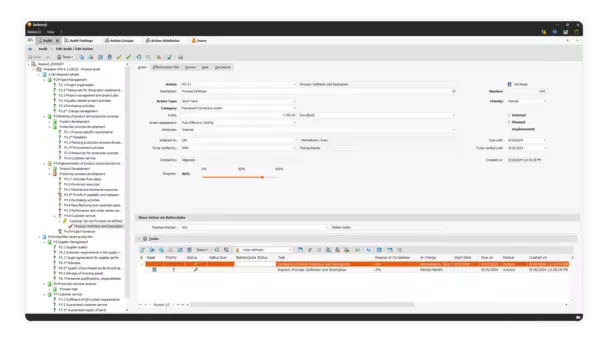
Audits allow you to ensure that your medical devices comply with strict regulations. You can manage all your audits efficiently in BabtecQ.
Audit management is essential for quality management. Strict regulations require regular audits to ensure product conformity in accordance with relevant guidelines. Audits identify weaknesses and enable continuous improvement. Customer satisfaction and reputation are strengthened as trust in high-quality medical products is established.
Manage internal and external audits in a centralized location – with the audit management of the BabtecQ QM software, this quickly becomes self-evident.
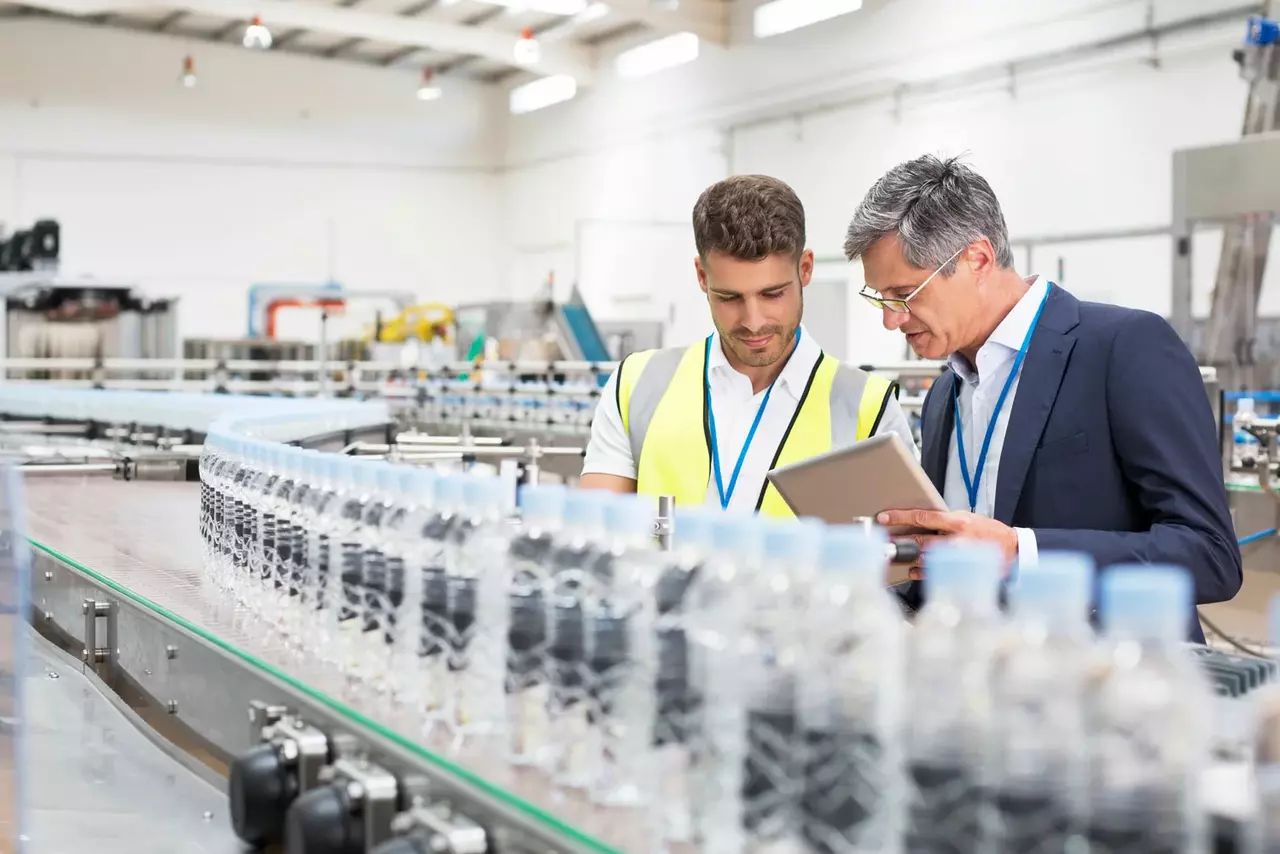
Enveloped in Quality – Writing a Success Story with QM Software from Babtec.
The Cherry on Top: The Relevance of Quality Management
A Contribution to the Success Story – QM
- Product safety and consumer protection: In the consumer goods industry, the safety of products is of paramount importance as they are used by end consumers. Quality management ensures that products comply with legal regulations and quality standards.
- Reputation and brand image: The quality of products and packaging contributes directly to a brand's reputation. Consistent product quality and appealing packaging strengthen consumer trust and contribute to a positive perception of the brand.
- Customer satisfaction and repeat purchases: Quality management makes it possible to manufacture products that meet the needs and expectations of customers. Satisfied customers are more likely to buy products from the same brand repeatedly, which strengthens loyalty and promotes business success.
- Product consistency and innovation: Quality management processes ensure consistent product quality across different batches. This enables companies to introduce innovations in products or packaging without compromising quality.
- Global markets and regulations: In today's globalized world, products often have to comply with international regulations and standards. Quality management ensures that products fulfil these requirements and enables companies to operate successfully in different markets without risking legal problems.
Guidelines & Standards
Consumer goods of all kinds and packaging for food, pharmaceuticals, cosmetics and other products - the consumer goods and packaging industry is as diverse as the number of relevant standards in the sector. Examples of relevant guidelines are
- ISO 9001 for an effective quality management system
- ISO 22000 with specific requirements for food safety management systems
- ISO 13485 with specific requirements for the manufacture of medical devices
- ISO 14001 for an environmental management system that promotes environmentally conscious behaviour and the adoption of more sustainable practices
- ISO 15378 with specific requirements for quality management systems for the manufacture of primary packaging for medicinal products
- ISO 22002-4 with specific requirements for preventive food safety programmes
- ISO 11607 with specific requirements for the materials and systems of sterile barrier packaging for medical devices
- BRC Global Standard for Packaging and Packaging Materials with requirements for suppliers of packaging for the food and consumer goods sector to ensure product safety
- FSSC 22000 for food safety, specifically for manufacturers of food packaging