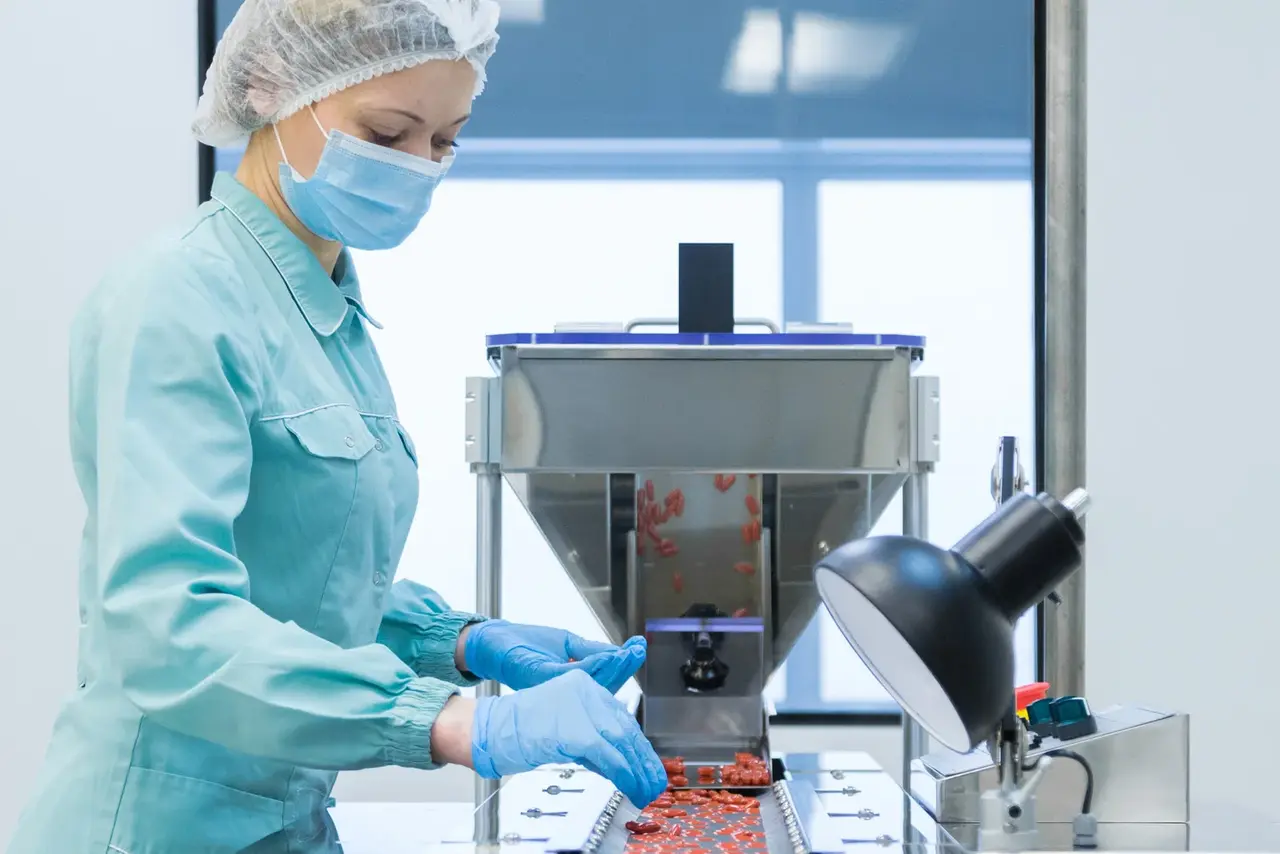
Quality Management in the Medical Technology & Pharmaceutical Industry
References from Medical Technology & Pharmaceutical Industry
QM Solutions for Medical Technology
Failure Mode and Effects Analysis (FMEA)
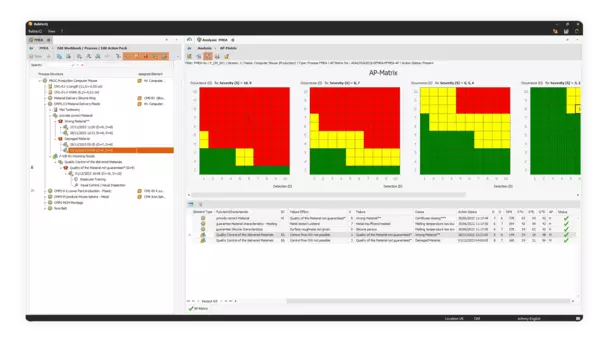
You create FMEAs in BabtecQ on the basis of the proven seven steps.
FMEA is indispensable in medical technology: risk assessment ensures maximum product safety and complies with strict regulations. Potential failures are identified at an early stage, quality is improved, costs are reduced and innovation is promoted. The documentation also increases transparency in the relevant audits.
Use the FMEA in BabtecQ to bundle valuable knowledge about products and processes in addition to the risk analysis.
Incoming / Outgoing Goods Inspection
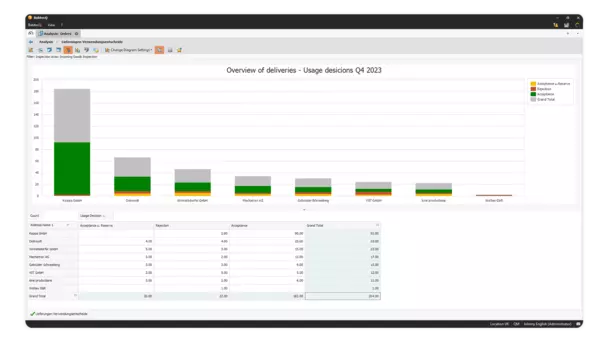
With BabtecQ, you can create clearly structured, efficient inspection sequences and support the correct execution of the inspection with visual assistance.
In medical technology, product safety is of the utmost importance. Incoming goods inspections ensure that incoming materials meet the required standards. Outgoing goods inspections ensure that only faultless products are delivered to customers.
This usually involves a great deal of effort. BabtecQ supports you with the incoming goods inspection / outgoing goods inspection and enables you to carry out the inspections efficiently.
Complaints Management
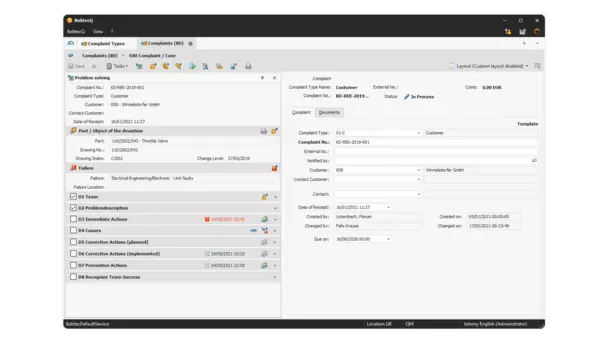
In BabtecQ you process complaints with Ishikawa diagrams, workflow support and 8D reports.
Complaints can indicate potential safety risks or quality defects. Effective complaints management in the medical technology industry enables the rapid identification and rectification of such problems to ensure patient safety.
Take the opportunity to optimize your own processes through complaints and claims. Complaint management in BabtecQ supports you in this.
CAPA Management
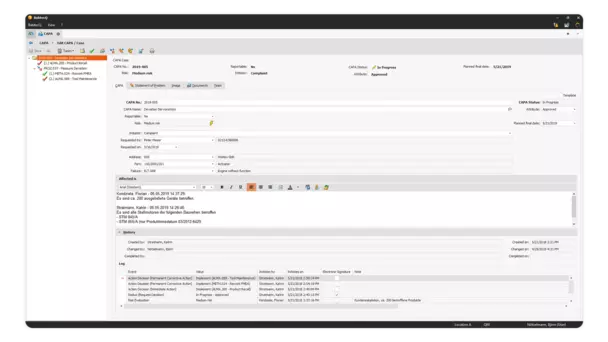
Keep your CAPA process under control with BabtecQ and document it comprehensively.
Product defects are annoying in any industry, but in the medical technology sector, even the smallest failures can have devastating consequences. CAPA management ensures product integrity in accordance with strict regulations and guarantees safety and efficiency. The identification and elimination of failures, prevention of future problems and continuous quality improvement are central to this.
Promote a culture of continuous improvement with CAPA management in BabtecQ and contribute to long-term excellence in product development and manufacturing.
Audit Management
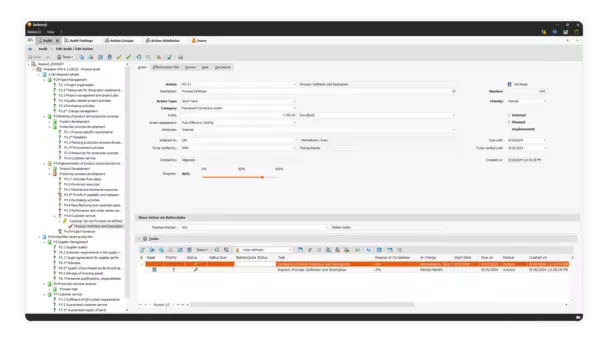
Audits allow you to ensure that your medical devices comply with strict regulations. In BabtecQ, you can manage all your audits efficiently.
In medical technology, audit management is essential for quality management. Strict regulations require regular audits to ensure product conformity in accordance with MDR, FDA and other guidelines. Audits identify weaknesses and enable continuous improvement. Customer satisfaction and reputation are strengthened as trust in high-quality medical devices is built.
Manage internal and external audits centrally – with the audit management of the BabtecQ QM software, this quickly becomes self-evident.
Task Management / Action Management
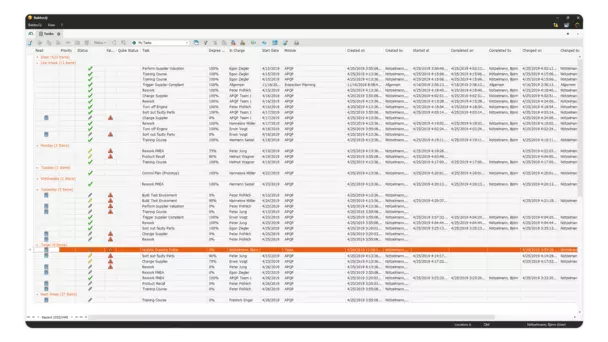
Whether immediate actions implemented, corrective actions introduced or preventive actions: In the dialog for processing an action, you document relevant information in a central location.
Products are often manufactured in complex production processes that involve a large number of steps and components. Failures can easily creep in and lead to quality deviations. Effective action management makes it possible to quickly identify and analyze deviations and initiate appropriate corrective actions.
Use the task and action management of the BabtecQ QM software to centrally manage and track your tasks and actions.
Qualification Management
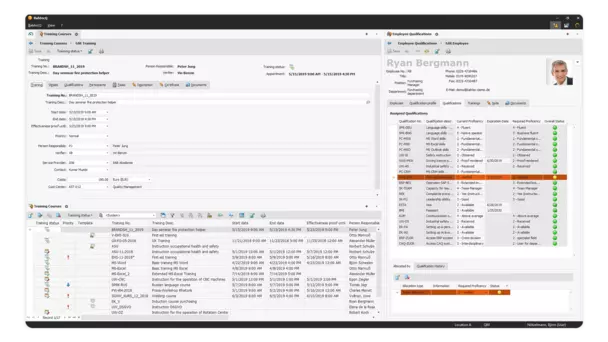
Qualification and training management in BabtecQ.
Regularly updating the qualifications and competence levels of all employees and maintaining an overview is very time-consuming. Quick and uncomplicated access to the required entries and convenient handling of training actions are therefore worth their weight in gold – both in everyday life and during audits, as standards such as ISO 9001 in quality management require proof of competence and effectiveness to be provided at regular intervals.
The qualification and training management in BabtecQ uses clear symbols in the qualification matrix to show you whether your employees have the required qualifications and notifies you if they need to be renewed soon.
Document Control
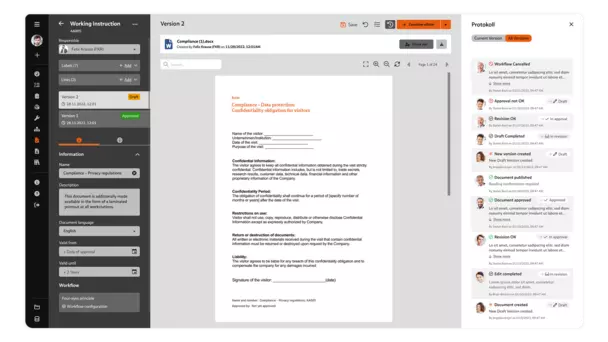
The “Document Control” software module takes care of the paperless distribution of documents for you: With just a few clicks, you can make the completed and approved documents available to users via your company network.
Standards such as ISO 9001, IATF 16949 and ISO 13485 require documented information to be managed within the company in a targeted manner.
The document control in BabtecQ also supports your company beyond QM by allowing all relevant documents to be viewed, edited and controlled easily throughout the entire company network.
Checklists
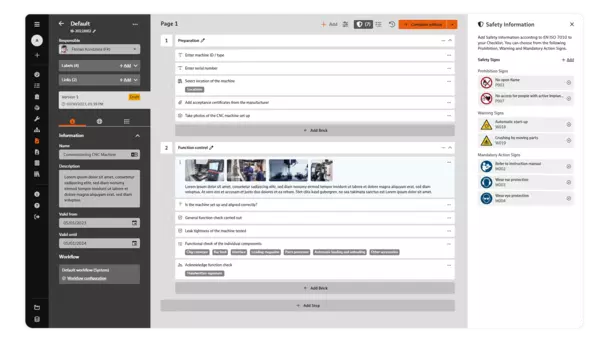
Creating checklists in BabtecQ Go is child's play thanks to the no-code modular system.
Commissioning, process sequences, assembly instructions, acceptance inspections: There are certainly many use cases in your company where checklists can provide effective support.
In the browser-based BabtecQ Go, you can easily digitize, share and use all your checklists. Standardize processes and create transparency for your employees. All the knowledge gained from your records is reliably incorporated into your continuous improvement process (CIP).
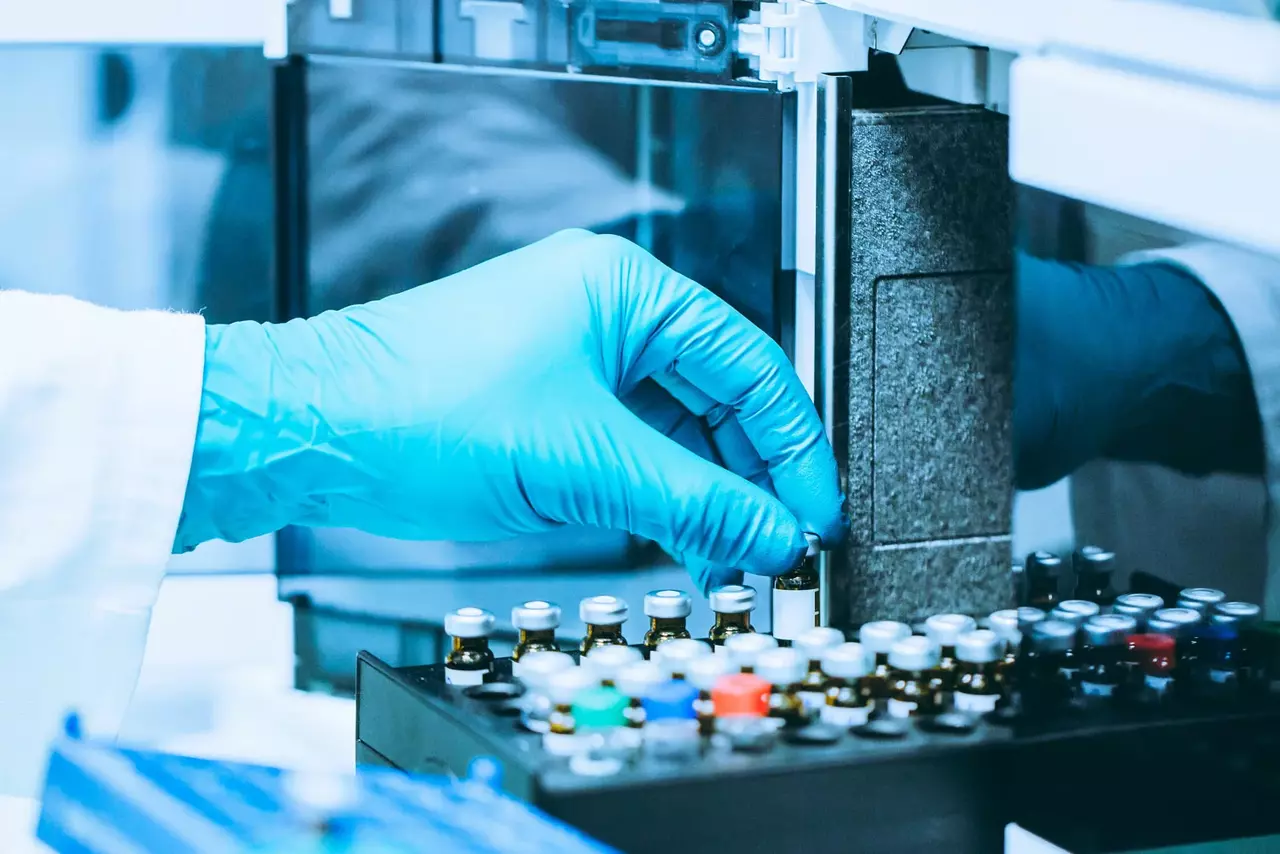
Your Commitment to the Health of Numerous Patients – Write a Success Story with QM Software from Babtec.
Precision Work for Precious Lives: The Relevance of Quality Management
A contribution to the success story – QM
- Patient safety and health: Quality management ensures that products and devices meet the highest standards. This minimizes the risk of malfunctions or improper use.
- Regulatory requirements: The medical technology and pharmaceutical industry is subject to strict official rules and regulations. A quality management system enables companies to comply with these regulations and obtain the necessary approvals and certificates to bring products to market.
- Reputation and trust: Patients, doctors and medical facilities rely on products that are consistently high quality and safe. Effective quality management strengthens the trust of stakeholders and contributes to the long-term reputation of the company.
- Product development and innovation: Structured quality management promotes continuous improvement, which in turn encourages innovation and the introduction of new technologies.
- Risk management: The identification and assessment of risks is essential in the medical technology and pharmaceutical industry. A quality management system helps to identify and minimize potential risks associated with products, processes and supply chains. This helps to prevent undesirable events and limit the impact of failures
Guidelines & standards
There are probably few industries in which the quality of the products manufactured has such a significant impact on the lives of customers, or in this case patients, as in the medical technology and pharmaceutical industries. It is therefore not surprising that there are strict guidelines to comply with. Examples of this are
- ISO 9001 for an effective quality management system
- ISO 13485 for an effective quality management system that is specifically geared towards the manufacture of medical devices
- ISO 14971 for the application of risk management to the development, manufacture and use of medical devices
- GMP (Good Manufacturing Practice) for the manufacture of medicinal products
- ICH Q9 developed by the International Conference on Harmonization (ICH) for quality risk management in the pharmaceutical industry