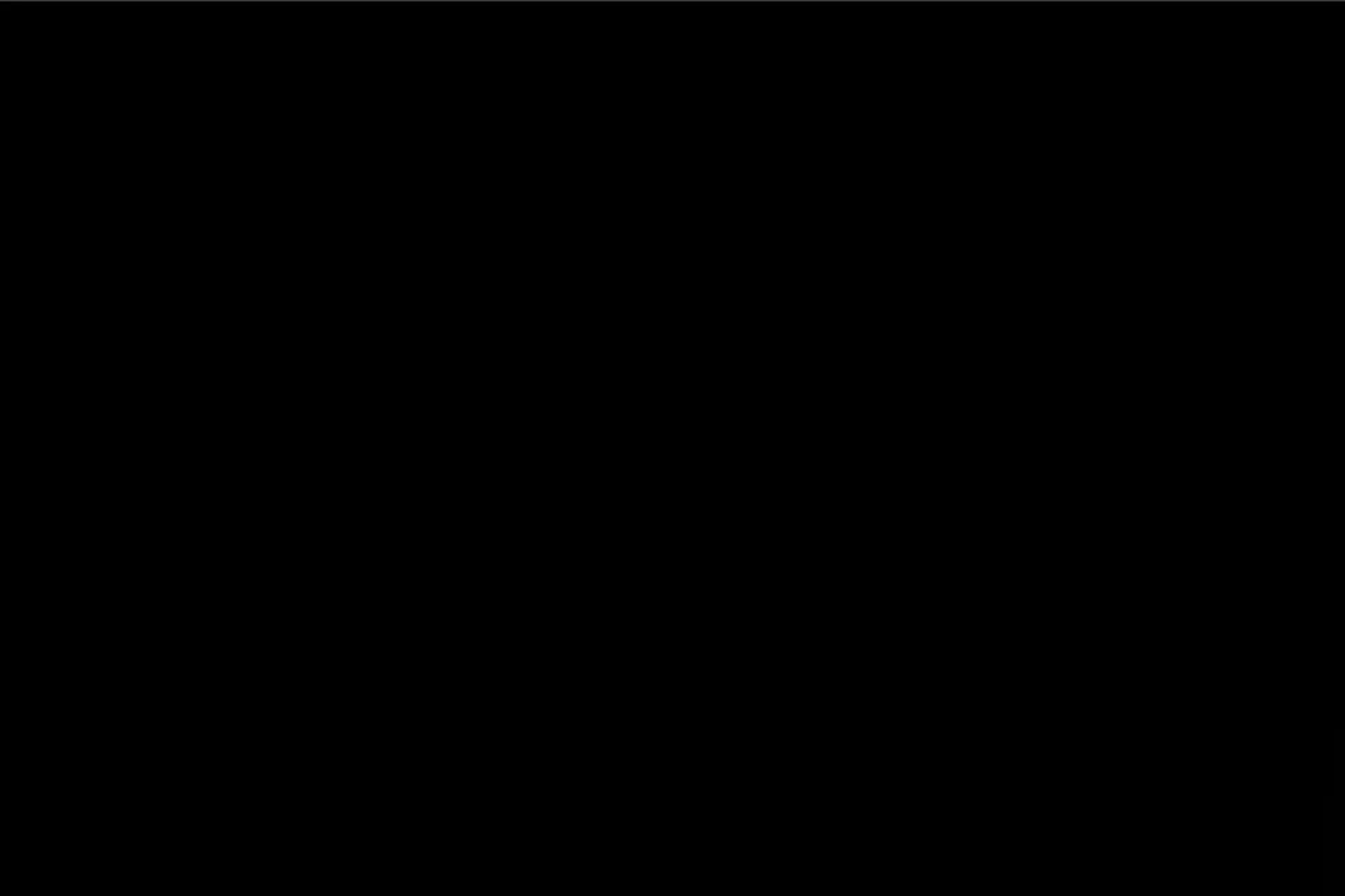
Software for Gage Management and Gage Capability Test
The "Gage Management" and "Gage Capability Test" Modules from Babtec
Capable gages are a prerequisite for objective assessment of measurement results and the decisions based on them. For effective quality assurance, the gages must therefore also comply with norms and standards. Use the convenient options of Gage Management to safeguard the quality of the measurement processes on the one hand and to consistently monitor the quality of gages and measuring equipment on the other. In this way, you will ensure the trustworthiness of your gages.
Safeguard the Quality of Your Inspection Results
In addition to Gage Management, the gage capability test (PMFU) provides evidence for a gage or inspection system that it is suitable for a specific measurement task under real operating conditions. That task depends not only on the device but also on the operating personnel. The suitability of a gage is determined by its accuracy, linearity, stability, traceability and repeatability.
Stay on Top of Things and in Control
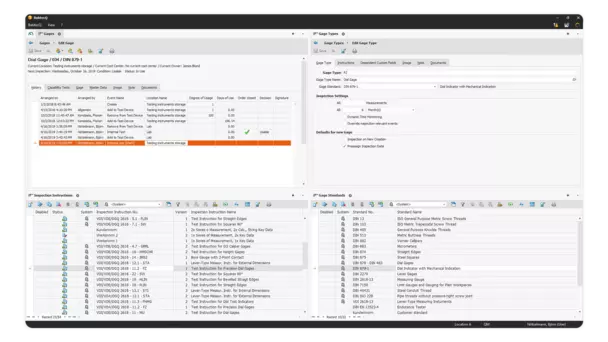
Gage Management in BabtecQ
With Gage Management, you receive a comprehensive instrument for the clear management, monitoring and maintenance of your gages. Each gage receives a unique identification number and is assigned a gage type based on its design. The data management is supported by using catalogs, e.g., for gage type, location or status. Each status or location change (e.g., during inspection or maintenance) is traceably documented via an entry in the gage history.
Inspections should always take place at reasonable intervals so that only gages with ensured capability are used. Depending on the task and usage site, individual gages may be subject to different stresses and wear. If, for example, there is increased wear on a certain gage, the set time interval for the device in question can be dynamically adjusted.
Record Results Manually or Automatically
Instructions are based on current guidelines, and the required standards also serve as the basis for determining the target specifications for each gage. Users can of course also use the existing instructions as a template for their own or specialized inspection instructions. For internally performed calibrations or control checks, results can be recorded manually using a keyboard or automatically via interfaces for importing measured values directly from the gage, measuring machine or inspection device. All saved results can be used for creating inspection certificates or reports. Furthermore they can serve as the basis for determining important key figures.
Ensure Gage Capability
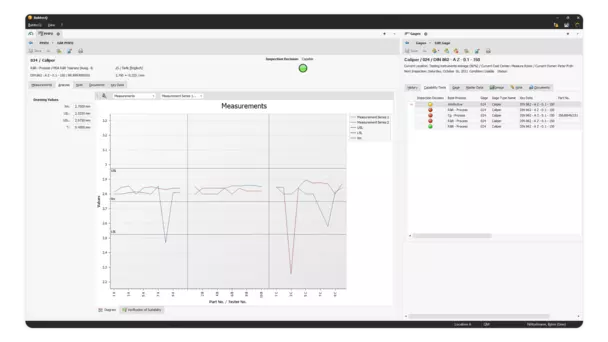
Graphical processing of the results already during the PMFU execution
Gage capability must already be ensured when you release products and production processes during the development of new products. Companies are therefore required to provide evidence of gage capability tests for every gage that is used in series production. With our wizard, all relevant key data that you require for the accurate testing of your gage capability is guaranteed to be fully recorded.
Reduce the expense of gage capability tests and measurement uncertainty considerations as part of verifying the suitability of the inspection process using predefined and standardized processes according to current guidelines. The assessment of gage capability automatically takes place immediately after the test is completed.
Companies That Already Rely on Babtec
From Medium-Sized Family Businesses to International Corporations
Your Contact to Us
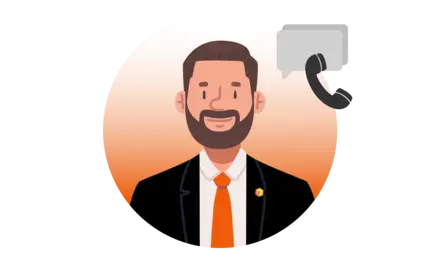
Would you like more information about our products, perhaps even in a personal consultation? Then please feel free to contact us!
You can reach us at the following times:
Monday–Thursday, 9:00 a.m.–4:00 p.m.
Friday, 9:00 a.m.–1:00 p.m.
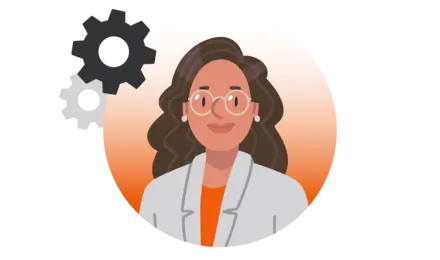
Are you already using our software and need support? Then please contact our support team directly.
Our colleagues will be happy to help you during our service hours:
Monday–Friday, 8:00 a.m.–5:00 p.m.